1. INTRODUCTION
Principles of conservation and restoration of cultural heritage state that lacquerware conservation should have to use original materials in traditional way. Therefore, the materials for restoration are determined as per the structural characteristics and damage type, and the actually damaged portions are being repaired and restored according to researches (Jang, 2016). Use of lacquer is required for lacquerware conservation, but the drying conditions of lacquer are extremely strict to result in difficulty in applying it to lacquerware conservation. High temperature and high humidity are known as the best hardening conditions for lacquer. Toishi and Kenjo (1970) explained that lacquer is dried in the relative humidity of 80-85% at 0-30°C, while Son (2006) proposed relative humidity of 60-80% at 20-28°C as the hardening conditions for lacquer.
Lacquer hardens and dries in two stages in the hardening conditions. As an oxidase included in lacquer, laccase acts as a catalyst in steam to oxidize urushiol, and lacquer dries through polymerization and the lacquer film is formed through continual automatic oxidization of urushiol and oxygen (Kenjo, 1986; Kim and Lee, 2002). Oxygen is essential for this hardening process, and the urushiol functional group plays a significant role (Choi and Kim, 2018).
Although the hardening conditions and mechanism have been studied, they are not easily applicable to lacquerware conservation. First, the compositions and contents of lacquer vary according to its place of origin and extraction period, and its drying characteristics and conditions vary too much to acquire certain results. Also, as it is difficult to maintain certain temperature and humidity in the lacquer drying rack (lacquer field) used by conventional craftsmen, the accurate characteristics of lacquer films cannot be identified. Therefore, it is important to know the characteristics of lacquer being used for conservation and set the drying conditions as per the desirable features of lacquer film. However, there have been little detailed studies on various characteristics of lacquer films according to the composition and drying conditions.
Therefore, this study designs a ‘humidity control machine’ that offers constant temperature and humidity, and exposes the two frequently used types of lacquer to their drying conditions to analyze their drying speed and optical characteristics of lacquer films depending on the contents of the major components and predict the results of lacquer paint films. This study also proposes how to appropriately handle lacquer, the natural material which has various compositions to make durable layer.
2. MATERIALS and METHODS
From the past, materials of Korean traditional furniture included pine, fir, blacked persimmon, and palmate maple, among which pines were used most frequently (Kim and Park, 2005). Therefore, this study selected Korean pine (Pinus spp.) as specimens, which was cut into the length of 7 cm, width of 22 cm, and thickness of 0.7 cm and dried in a moisture content of 13% or less. Also, its surface was ground to make it even.
Slightly varying by case, natural lacquer is in an emulsion state as a compound of pyrocatechol (derivative from phenol, 60-65%), moisture (20-25%), polysaccharide (consisting gum, 5~7%), glycoprotein (consisting nitrogen substance, 2~5%) and laccase (oxidase, 1%) (Cho, 2000; Kim, 2007). The types of pyrocatechol vary by tree species and climate, and the catechol of lacquer from rhus verniciflua stokes growing in Northeast Asia is urushiol (Anzai, Lu, Phuc, Miyakoshi, 2014). Also, although lacquer is extracted from same area, its composition varies according to the place of origin and extraction period.
Therefore, to compare and examine two types of lacquer with different compositions, two types of lacquer were selected for conservation, and their impurities were eliminated to use them as filtered natural lacquer. Korean lacquer from Wonju, Gangwon-do, and Chinese lacquer were used to make the specimens.
The natural lacquer of the two types were heated to remove moisture, and acetone was added to separate urushiol, and then their content proportions were analyzed (Song and Han, 2001). Moisture and urushiol were separated from these two lacquers and the contents were measured two times. The result showed average 13.4% higher content of urushiol in Korean lacquer than Chinese one (Table 1).
Type of lacquer | Time | Water | Urushiol | Etc |
---|---|---|---|---|
Korean | 1st | 27.3 | 60.8(83.6) | 11.9(16.4) |
2nd | 27.8 | 62.0(85.8) | 10.2(14.2) | |
Chinese | 1st | 24.6 | 51.8(68.8) | 23.6(31.2) |
2nd | 24.1 | 56.0(73.8) | 19.9(26.2) |
This test was conducted through initial coating (Chochil), middle coating(Jungchil), and upper coating (Sangchil) as per the production process of lacquerware. Here, no other purification process was done on the lacquer other than impurity removal through fine filter net. Initial coating refers to applying watery lacquer to the base wood (specimen) to be absorbed on the wood in the first place to prevent moisture absorption of background wood and enhance the adhesion of next coating. Middle and upper coatings with a higher concentration of watery paint form a lacquer film of lacquer and determine its characteristics.
Half of a specimen's surface was applied with Chinese lacquer, and the other half was applied with Korean lacquer. The preliminary test showed that the specimens with 1:2 concentration ratio between lacquer and turpentine oil (diluting agent) for initial coating and 1:1 for middle and upper coating were the most suitable to observe the drying speed and paint film formations. As initial coating absorbed in the wood to make it difficult to measure the drying conditions, middle coating and upper coating were applied in sequence to the specimens that had completed initial coating in batch for the test.
To test the drying conditions, various conditions should be equally prepared and constantly maintained in the test space. However, although temperature control was available in the ‘chiljang’, a lacquer drying method for lacquer, moisture should be manually supplied, and it was difficult to constantly maintain humidity (Fig. 1). Also, convection did not occur in the internal space only to cause moisture congestion and resulted in uneven temperature and humidity. Therefore, a ‘lacquer conditioning dryer’ was designed and used in the experiment (Fig. 2). The 'lacquer conditioning dryer' consists of an air supplier (Fan) to supply humidity and warmth into the chamber, of which temperature and humidity were measured to run the pan according to the environmental changes. A perforate plate with countless holes was installed between the chamber and pan to allow fine air supply. As air supply from the pan was made to the lacquered target almost windlessly through the perforated pan, rapid moisture change was inhibited to dry lacquer in an environment with certain temperature and humidity.
The preliminary test confirmed that temperature and humidity were more constantly maintained than chiljang as the existing drying field (Fig. 3, Fig. 4).
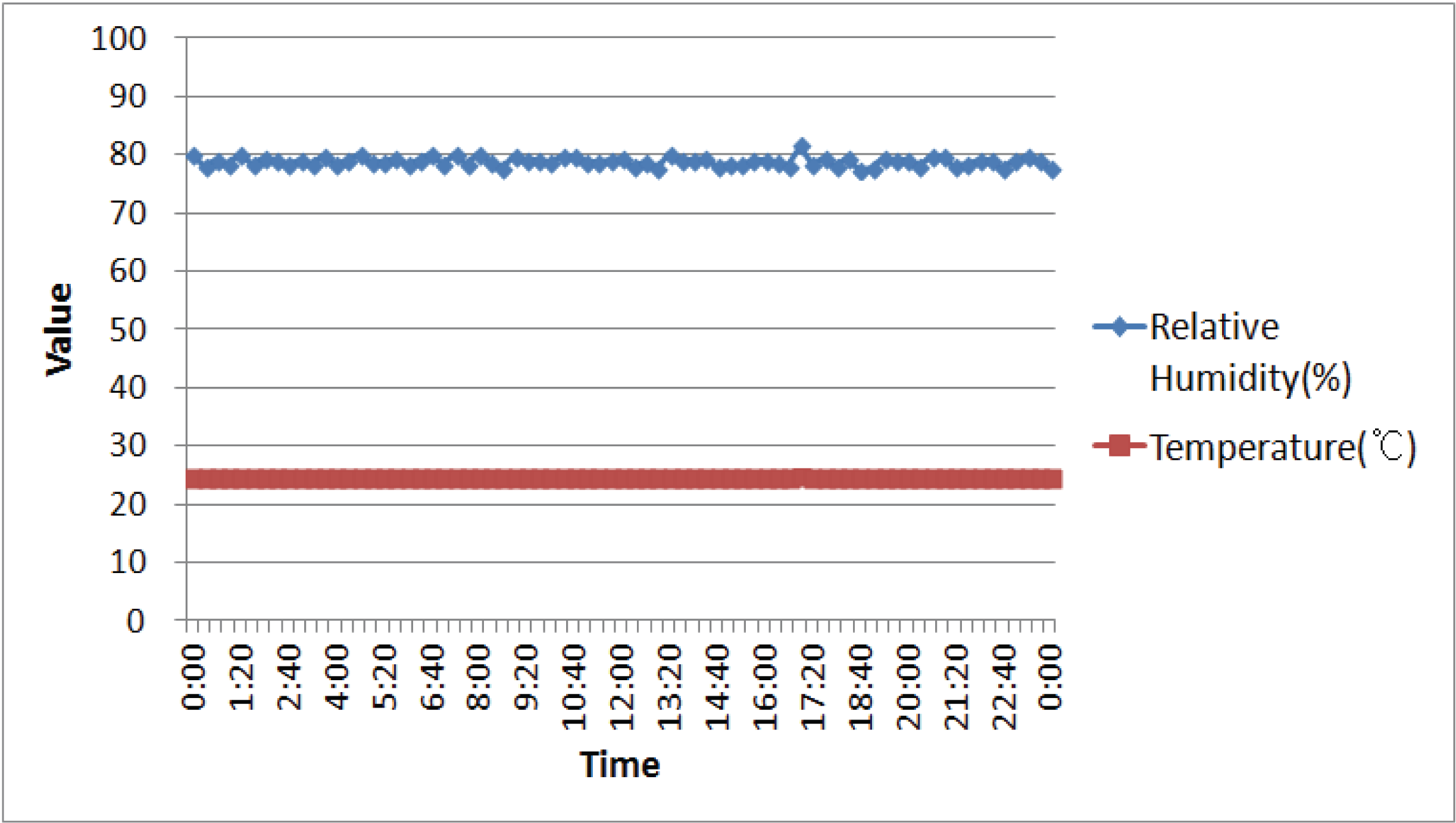
Temperature of the humidity control machine was set to 24 ± 1 °C, while humidity was set to 60%, 70%, 80%, and 90%. Three specimens were exposed to such environment in order to dry Jungchil (Middle layer) and Sangchil (Upper layer). Thus in this study, achieving up to Sangchil formed triple lacquered layer. The drying aspect was checked with the lapse of time, and the curing drying time at which the lacquer was completely dried was measured at intervals of 3 hours. The test for confirming the dryness was carried out using a drying test in accordance with KS M 5000. In KS M 5000-2511 drying condition and test method, drying hard condition indicates that there is no stretch or wrinkle of the layer and no other abnormality when it is twisted at an angle of 90 degrees while holding the arm vertically to press hard with thumb.
To investigate whether two different types of lacquer with different urushiol contents exhibit different optical properties depending on the drying rate, which varies by drying condition, Jungchil and Sangchil were applied to the specimen of Korean and Chinese lacquer in the environment of relative humidity of 90% (humidity control machine) and the properties of the dried lacquer layer were evaluated. At the same time, lacquer layer was obtained by exposing three specimens to the created environment. The same procedure was repeated twice and each three specimens group was divided into 90% (A) and 90% (B). Two drying conditions were additionally prepared for comparison and triple specimens were exposed and evaluated in the same way. First, properties of the specimens dried by exposure to a relative humidity of 60% in the humidity control machine for 30 days were measured. Regarding the specimens exposed to 60% of the environment for a long time, drying of Jungchil occurred at a very slow rate from the surface and thus, the application of Sangchil was difficult. Accordingly, only Jungchil was used as a target sample. Second, specimen of which Sangchil was dried at saturation humidity with relative humidity of 99% or more after Jungchil was cured and dried at 80% relative humidity in the humid control machine.
The cross section of the lacquer layer was observed through a microscope. Regarding lacquered specimens, seven sections which were cut to the same thickness of 20 μm were placed on a preparat and then, preparat for layer observation was prepared. The thickness and color of the layer were confirmed through the same light amount of transmitted light at a high magnification (400 magnification) using an optical microscope (Eclipse Lv 100, Nikon, Japan).
In this study, the brightness and gloss of the surface of each lacquer layer were measured with a spectrophotometer (A-6800, BYK, USA). Brightness is expressed as L value and gloss as G value. Brightness is the intensity of color, expressed as a number from 0 to 100 according to the CIE Lab color space. The higher the number, the brighter and the closer to 0, the darker. Regarding gloss which is a measure of reflected light, resultant value is represented by a quantitative value from 0 to 100 when the incident angle of light is 60°. Since the specimen used is a preformed wood plate, the inherent gloss of the wood may affect the surface gloss of the lacquer overlaid on top. Accordingly, the brightness and gloss of the Sangchil layer with lacquered layer which was overlaid three times through Chochil, Jungchil, and Sangchil were compared.
3. RESULTS and DISCUSSION
The humidity control machine was used to measure the time when curing drying was completed at intervals of 3 hours. As a result of the measurement, it was found that both Korean and Chinese lacquers dried faster when the relative humidity was near 100% at 24 ± 1°C. Furthermore, at 24 ± 1°C and less than 70% relative humidity, no drying as setting to touch occured within 336 hours (14 days) and thus, it was confirmed that it takes longer than that. The specimens simultaneously exposed to the same environment showed the same drying rate in the triple samples. As a result of illustrating the drying rate of Korean lacquer and Chinese lacquer dried at the same time in a graph, Korean lacquer was confirmed to be dried 2-3 times faster than Chinese lacquer (Fig. 5).
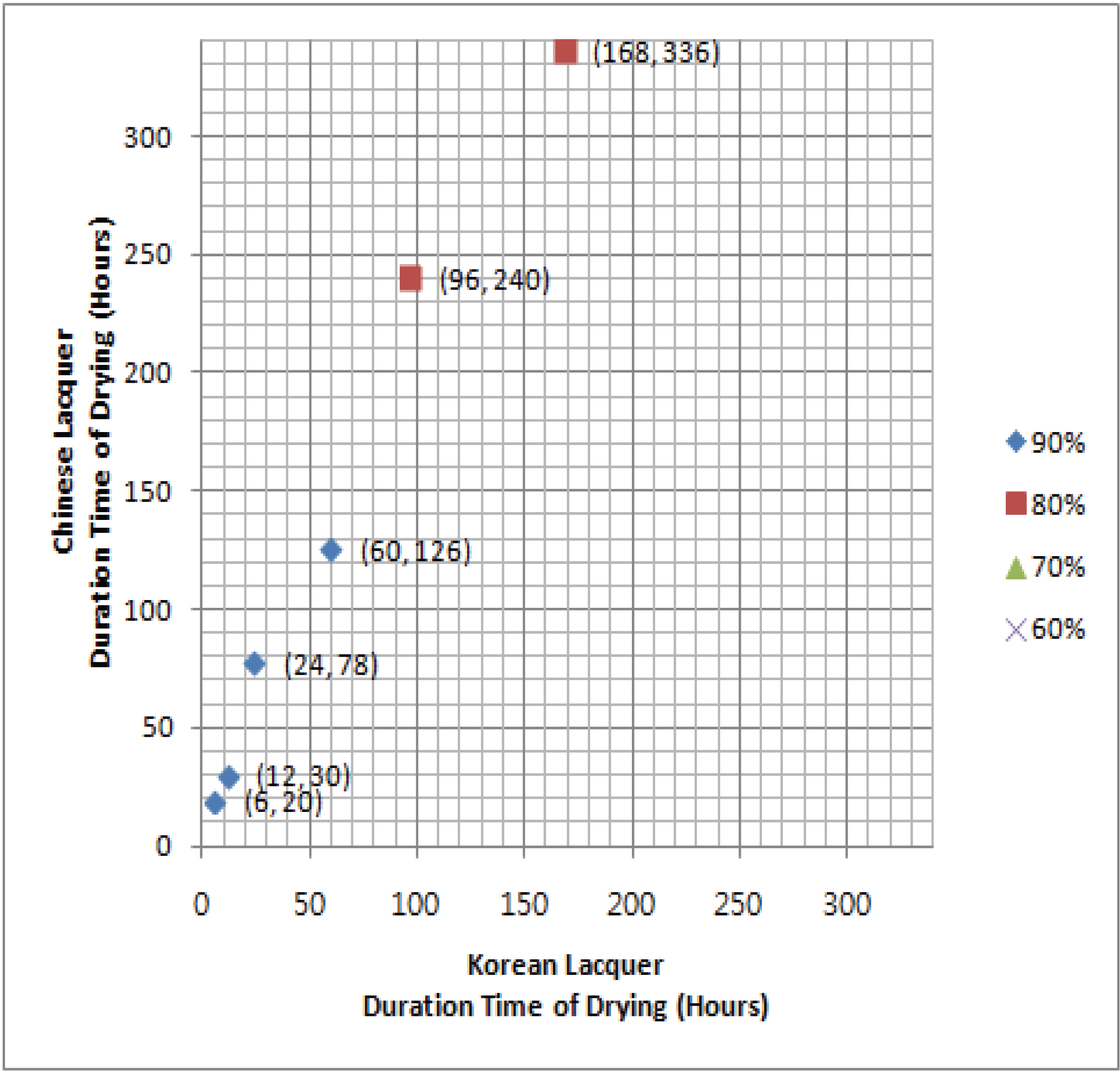
The specimens dried under various drying conditions were all cut to a thickness of 20 μm to prepare a section. They were observed with the same amount of transmitted light. As a result of the observation, The average height of the lacquer layer of Jungchil formed on the specimen was about 16 μm. In addition, the average height of the lacquer layer on Sangchil portion was about 31 μm. All of the specimens were found to have uniformly formed Jungchil and Sangchil over the Chochil that had penetrated into the wood substrate. As a result of comparison of Korean lacquer and Chinese lacquer dried at the same time, in case of Korean lacquer, the color is more intense than Chinese lacquer (Fig. 6). The Jungchil layer of the specimen dried over a long period of 30 days at a relative humidity of 60% showed a very light color compared to the Jungchil layer of the specimen dried at 90%. Accordingly, it is judged that the drying by the oxidation polymerization reaction did not occur sufficiently (Fig. 7).
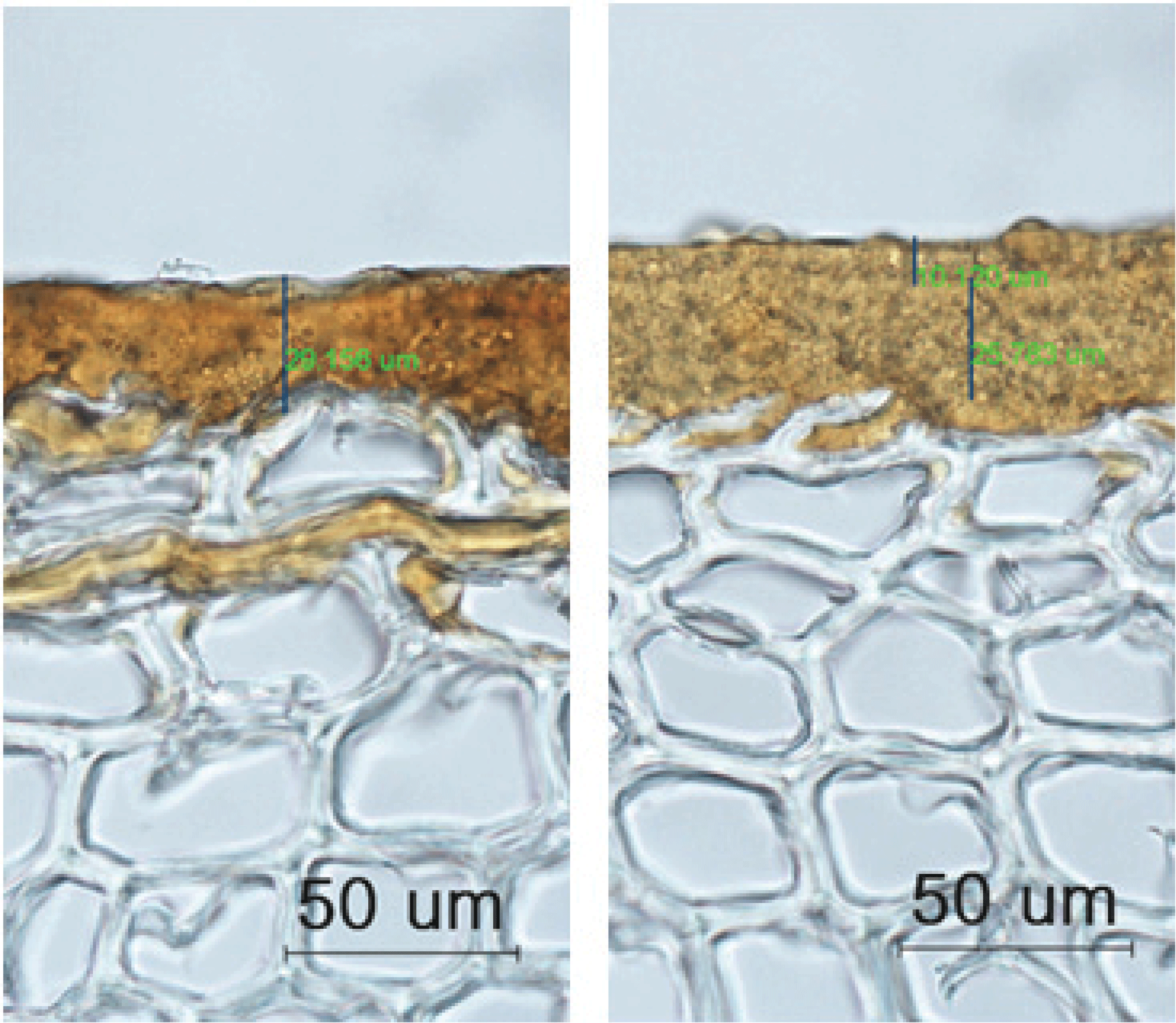
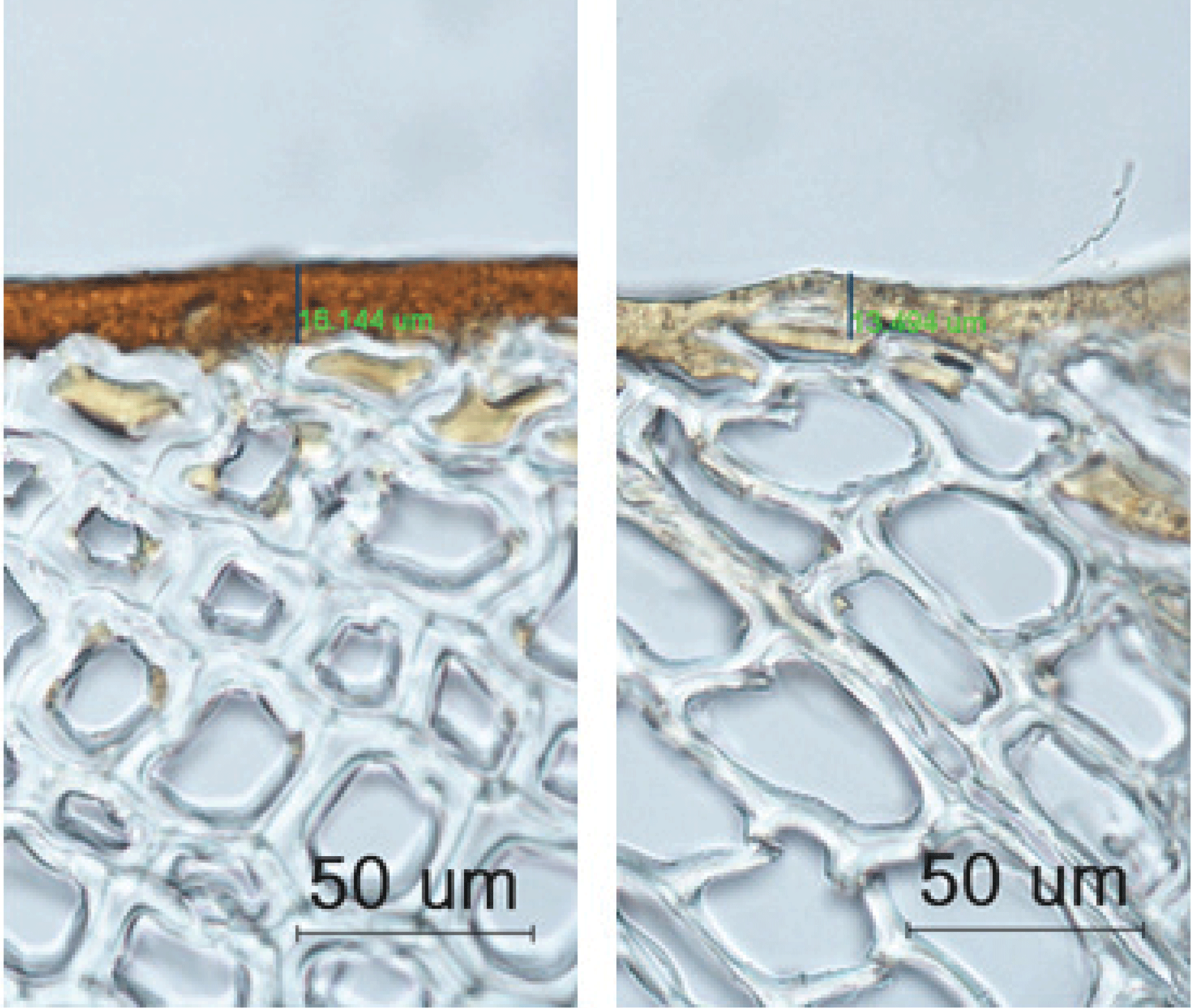
Moreover, the color difference between the Jungchil and Sangchil layers in the Sangchil part of the specimen dried at saturated humidity was apparent. Sangchil dried at 99% saturated humidity (less than 3 hours for Korean lacquer, and 18 hours for Chinese lacquer) showed darker color than Jungchil layer (96 hours for Korean lacquer and 240 hours for Chinese lacquer) dried at 80% (Fig. 8). It was judged that there was a difference in color of the layer depending on the drying speed.
The surface brightness and the gloss of the specimen layer were respectively measured, quantified and compared. For easy comparison, Sangchil layer sample's L value and G value, which are an intermediate value among the L value of brightness and G value of gloss triple specimens, are listed in the order of the fast drying time in graph below (Fig. 9, Fig. 10). Curing and drying completion time of Sangchil at relative humidity of 99% was less than 3 hours for Korean lacquer and 18 hours for Chinese lacquer. The following were targeted: 90 (A) Sangchil of which the curing and drying time was 6 hours for Korean lacquer, 21 hours for Chinese lacquer and 90(B) Sangchil of which the curing and drying time was 60 hours, and 126 hours, respectively.
Lower L value was associated with short drying time for both Korean Sangchil layer and Chinese Sangchil layer. It was confirmed that the L value of domestic lacquer was lower than that of Chinese lacquer in an environment with a relative humidity of 90%, Korean.
Although G value of 90%(A) of which drying time of the Sangchil layer is faster than that of 90%(B) at relative humidity of 90% is greater than 90%(B), G value of Sangchil layer dried at saturated humidity (99%) where drying time is the fastest was found to be low.
Thus, In both Korean lacquer and Chinese lacquer, the faster the drying time, the lower the brightness of the sample and the higher the gloss. However, it was confirmed that the lacquer dried at saturation humidity (99%) had a lower gloss of the surface.
4. CONCLUSION
In this study, we designed the humidity control machine that maintains constant temperature and humidity and by using this, examined the drying conditions of lacquer with different composition ratios under different drying conditions through drying condition experiment. The optical properties of the resulting layer were evaluated to obtain a technique for forming a drying condition for obtaining a lacquer layer during preservation of desired lacquerwares.
Through this study, it was confirmed that the humidity control machine can form a constant drying environment, and maintain it stable, and be utilized for lacquer drying. The gloss and chromaticity of lacquer layer were different according to the content of urushiol and the drying rate. The conclusions are as follows.
It was found that the drying rate of Korean lacquer of which urushiol content is about 13.4% higher (excluding moisture content) was 2 to 3 times faster than Chinese lacquer and the higher the humidity, the shorter the drying time. Under the relative humidity of 70% or less, the lacquer was not dried for 336 hours, and thus, there was a drawback that the ease of operation was poor. Long-term exposure (more than 30 days) results in drying of the surface, but it is difficult to judge that the lacquer is dried by oxidative reaction due to insufficient color change.
Further, it was found that Korean lacquer layer with high urushiol content has lower brightness than Chinese lacquer layer. In addition, it was confirmed that the faster the drying rate, the lower the brightness and the higher the gloss even though it is the same kind of lacquer. However, when it became close to saturated humidity, the lacquer was dried rapidly, and the brightness was greatly lowered, but the gloss was greatly decreased.
Therefore, drying rate can be predicted in accordance with drying conditions and major components of lacquer used when forming lacquer layer using lacquer during conservation and restoration of lacquerwares in the future, and the characteristics of the lacquer layer can be predicted depending on drying time. It is expected to be used as basic data.