1. INTRODUCTION
Currently, the domestic wood construction market is growing with an average of 15,000 houses built per year, and according to construction permit/construction statistics by Ministry of Land, Infrastructure, and Transport as of 2017, the number of wood construction and that of brick houses were 13938 and 7494, respectively, indicating the number of construction permits/constructions of wood construction is twice that of brick houses (MOLIT - Statistics of housing construction-Housing construction records. 2017).
The main materials used for wood construction are engineered wood such as dimension lumber and structural panel, whose performance needs to be certified to be used for wooden structures.
Among engineered wood, oriented strand boards (OSB) and structural plywood are mainly used for structural panels. These materials are mainly used as covering material for roof, floor and wall structures with reasonable price and suitable structural performance. OSB is a laminated composite material, which is regarded as an orthotropic material like wood, so it has facing with interlaminar shear and shear through the thickness in use. performance. The interlaminar shear is also referred to as rolling shear or planar shear since shear is caused by external forces applied along the plane of the panel (Shrestha, 1999).
Due to the structural characteristics of wood construction, these sheathing cover materials are placed on the joists and serve as the vertical load resistance component and as the horizontal load resistance component through the horizontal diaphragm structure. For the wall structures, they are used as the main members of the horizontal load resistance elements, so they should maintain proper structural performance.
The shear performance of the OSB was measured mainly by the shear test on between the OSB and the nail(Hwang and Park, 2008; Oh, 2013), rather than on the shear performance of the structural panel itself and to measure the shear stiffness of a LVL through a tensile test (Oh, 2013).
The shear performance test of such a structural panel itself is often omitted during quality control process, due to the difficulty of the shear performance test method itself and the cost required for the test (Fridley and French, 2000). However, as the use of OSB becomes more common in wood construction, the shear performance is becoming a major factor in structural performance due to lateral loads such as wind and earthquake, and needs to be considered (Nadir and Jerrold, 2007).
The direct shear performance test method for structural panels is ASTM D2718. In this test method, the 5-point bending load test method is widely used since it is simple and economical, and the shear performance can be directly measured through it (Thomas, 2004; Nadir and Jerrold, 2007). Sretenovic et al. (2005) conducted a comparative study on the rolling shear performance of plywood and OSB using the 5-point bending test and the EN 789 test, and the 5-point bending test method was applied to the structural composites such as laminated veneer lumber (LVL) and parallel strand lumber (PSL) as well as structural panels (Bradtmueller et al., 1998; Frank and Bruce, 2000; Fridley and French, 2000).
In particular, the 5-point bending test for composite materials is considered a very efficient method for measuring the interlaminar shear force of a oriented composite material, because the effect of shear stress on the entire specimen is very large and the bending stress is close to zero (Kim and Dharan, 1995).
In this study, the 5-point bending test was applied to the OSB and domestic plywood which are widely used in the wood construction site, and the rolling shear force was measured to conduct a comparative study on their performance.
2. MATERIALS and METHODS
The structural panels used in this study were four kinds, 1 domestic plywood and 3 imported OSBs, imported from Europe, Canada and Chile, respectively, and purchased from professional companies to be used as test materials. Table 1 shows the thickness, density and moisture content of specimens from each structural panel of 4 × 8 size.
The test specimens parallel to the longitudinal direction from each structural panel had the dimensions of thickness × width × length = 11 (plywood: 12) × 120 × 400 mm, while the test specimens perpendicular to the longitudinal direction had thickness × width × length = 11 × 120 × 290 mm (plywood: 12). Five test specimens were cut and randomly selected from each panel, a total of 15 test specimens were prepared in each type of panel. The specimens were conditioned at 20°C, 65% relative humidity for about 10 days before testing. Fig. 1.
For each prepared test specimen, in accordance with ASTM D 2718 method, the maximum load was measured at the time of failure using a universal testing machine (DTU 900-H) as shown in Fig. 2.
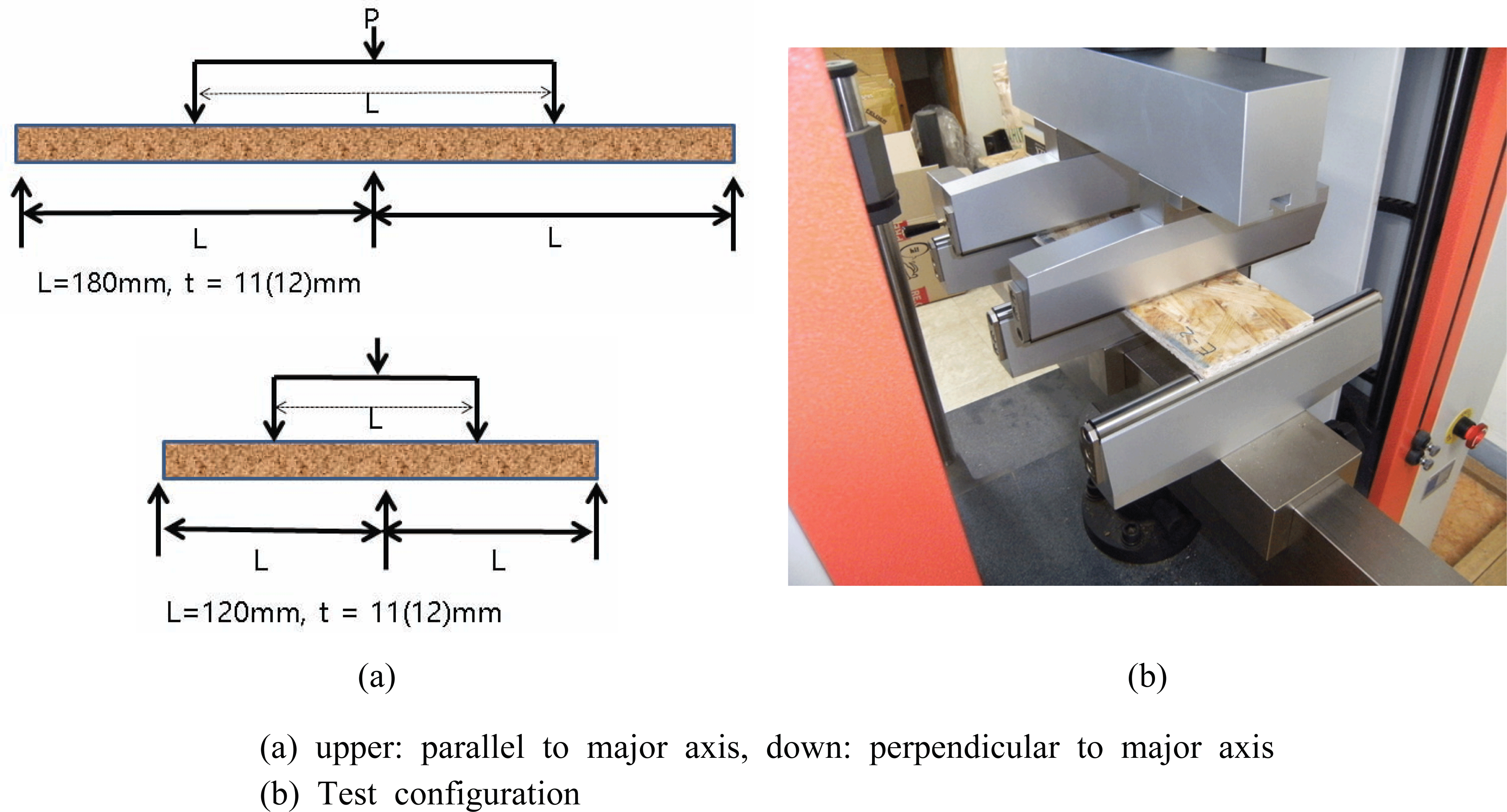
The span (L) of the test specimen parallel to the longitudinal direction of the panel in accordance with ASTM was 180 mm, which corresponds to 16 times the thickness of the minimum span, and the specimen perpendicular to the longitudinal direction was 11 times the thickness of the minimum span, 120 mm, respectively.
The load velocity at the test was 1.3 mm/min and the rolling shear strength (fv) of the structural panel was calculated according to the following formula using the measured maximum load.
P = Maximum Load (N), b = The width of specimen (mm),
d = The thickness of specimen (mm)
ANOVA test and Duncan's multiple test for data analysis were performed using SPSS statistical program to verify the statistical difference for each measured value.
3. RESULTS and DISCUSSION
The typical load-deflection curves for the 5-point bending tests are shown in Fig. 3. As shown in the figure, the plywood showed a tendency to continuously resist shear even after the primary failure, except for the case of delaminatiomof the adhesive layer. In the case of OSB, all of them showed rapid drop after reaching the maximum load due to failure by rolling shear.
Table 2 shows the rolling shear strength and maximum bending stress parallel to the longitudinal direction for each structural panel. As shown in Table 2, C/OSB, plywood, N/OSB, and E/OSB are the order of rolling shear strength when parallel with the longitudinal direction, and the maximum rolling shear strength for C/OSB is 1.90 N/mm2, the greatest of all.
Bradtmuller et al. (1997) reported that the mean rolling shear strength of OSBs with different widths and spans of specimens in the 5-point bending test was 0.81 N/mm2, while Shrestha (1998) and French (2000) reported 1.13 N/mm2, respectively, which shows that except for European OSBs, all values were high. This is thought to be due to the size and span conditions, such as the thickness and width of the specimen, and the directions.
Rolling shear strength perpendicular to the longitudinal direction was in the order of plywood, C/OSB, N/OSB and E/OSB, with plywood showing the greatest rolling shear strength of 2.38 N/mm2.
This tendency is different from the case of the rolling shear strength parallel to the longitudinal direction. Sretenovic et al. (2004) pointed out that the structure of the middle layer of the OSB is discontinuous, which suggests that the splitting due to the load easily occurs.
The significant difference between rolling shear strength of the panels was first verified by ANOVA test and then Duncan's multiple test was conducted. The result shows that in terms of rolling shear strengthparallel to the longitudinal direction, Chilean OSB showed the highest shear performance and there was no statistically significant difference in shear performance between plywood and Canadian OSB as shown in Fig. 4.
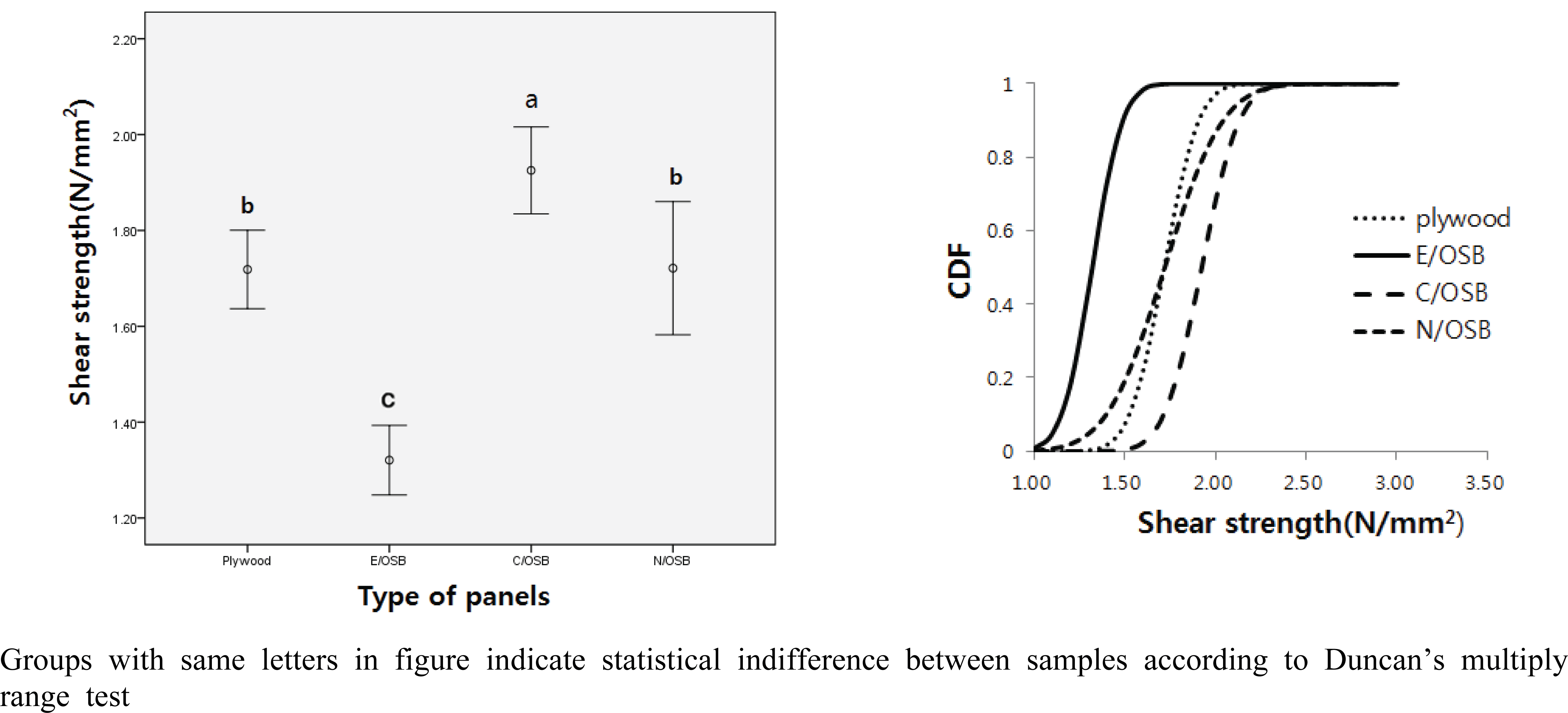
The lowest shear performance was found in European OSBs, and statistically significant differences were also found when compared to the three other panels. The shear strength between panels perpendicular to the longitudinal direction is shown in Fig. 5, indicating that the plywood showed the highest shear performance, with no statistically significant difference found when compared to the Chilean OSB.
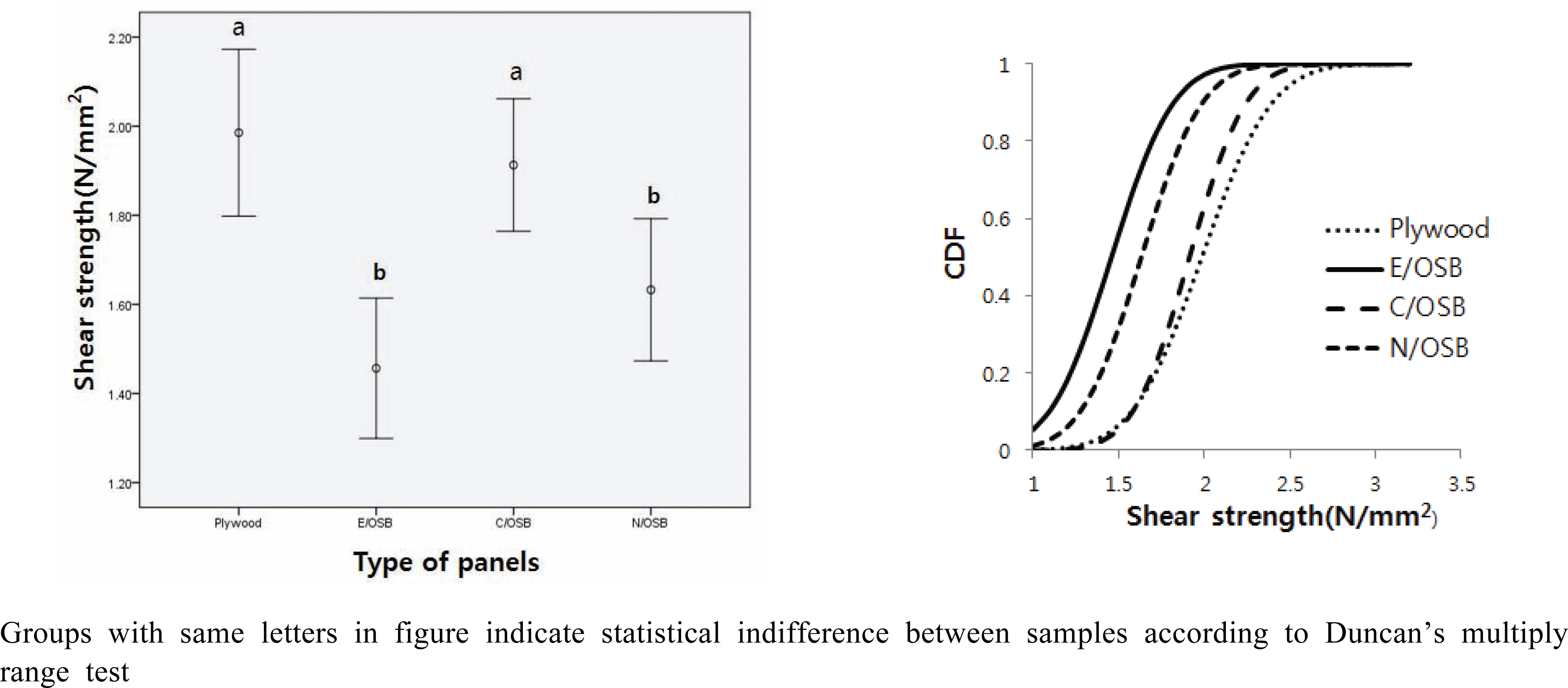
Bradtmueller et al. (1997) reported that the rolling shear force was 0.89 N/mm2 on average for the 23/32 inch OSB and that there was no significant difference according to the test direction, which was consistent with the result of this study.
Sretenovic et al. (2005) reported that shear performance of the plywood was higher than that of the OSB in the comparative study of the shear strength of plywood and OSB when 5 point load was applied. This is due to the density gradient in the OSB layer structure and the high ratio of middle layer with low density resulted in the weakened shear resistance capability.
The thickness of the their test specimens used was 20.5 mm for the plywood and 21 mm for the OSB. In the case of the OSB, the thickness of the middle layer with low density was 17 mm, which resulted in the increase of the density gradient. The thickness of structural panel used in this study is 11 mm (plywood is 12 mm), and the difference in the density between the surface and the middle layer is relatively small, so it is more influenced by the specific gravity.
No statistically significant difference was observed between the domestic plywood and the Canadian OSB, which was statistically verified to have the same shear performance when parallel to the longitudinal direction, and the Chilean OSB, which was statistically verified to have the same shear performance when perpendicular to the longitudinal direction. Therefore, it is considered that it is possible to yield the allowable stress of the same level as those of the two structural panels.
Table 3 and 4 show the failure mode and the ratio of each structural panel. As shown in Table 3, failure modes by rolling shear were observed in C/OSB, N/OSB, and E/OSB, and the ratio was 100%.
The Bradtmueller et al. (1997) showed that the rolling shear failure was 96-97% depending on the width of the test material regardless of the direction. The shear test by the 5-point bending test showed that most of the material failures were shear failure, and this study showed the same tendency.
In the case of plywood, the failure ratio by rolling shear was 47-53%, followed by the combined bending failure and shear failure, and the delamination failure of the adhesive layer was 13%. The shear failure of plywood and OSB both occurred between the points, and the failure due to the bending occurred at the center part of the specimen with vertical splitting.
The occurrence of failure between points is shown in Fig. 6. As shown in Fig. 6, the highest shear force is applied there in the shear force diagram showing the maximum shear force in this section.
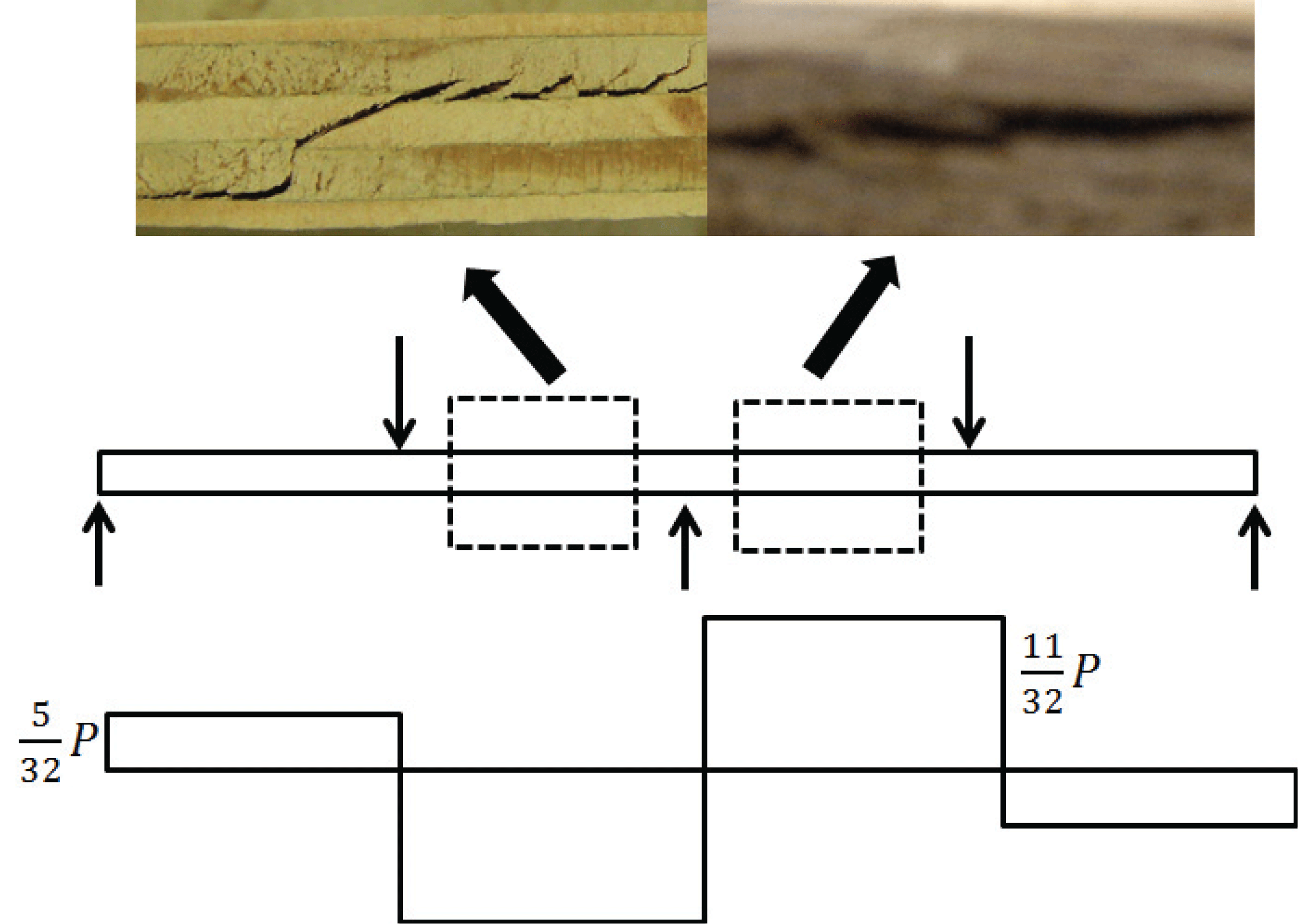
Since the shear strength of OSB depends on the weakest layer of middle layer with low density due to density gradient, it is thought that if shear stress exceeding the shear strength of middle layer is generated, delamination of adhesive layer occurs, and failure occurs at this part.
In the case of plywood with bending failure, as shown in Fig. 7, since the maximum bending moment occurs at the center, it is thought that failure occurs when the bending performance of the plywood is exceeded at this position.
4. CONCLUSION
The 5-point bending test method of ASTM D 2718 was used to determine the rolling shear force of imported OSBs and domestic plywood, which are currently used as typical cover materials in wood construction, and the results are analyzed.
The findings show that when parallel to the main axis, the highest shear force was 1.19 N/mm2 for Chilean OSB, and 1.67 N/mm2 for Canadian OSB, 1.71 N/mm2 for plywood, and 1.32 N/mm2 for European OSB which is the lowest value, respectively. No statistically significant difference was found.
In the case of perpendicular direction to the main axis, the shear force was 1.91 N/mm2 for Chilean OSB and 1.99 N/mm2 for plywood, representing the highest shear forces, and 1.63 N/mm2 for Canadian OSB and 1.46 N/mm2 for European OSB, with no statistically significant difference found. There was little difference between the both directions in each panel.
In the three kinds of imported OSB, all the failures were by shear, and in the case of plywood, shear, delamination of the adhesive layer, failure due to bending and shear, and so on were observed, indicating it is affected by its layer structure.
From these results, it is concluded that domestic plywood can be used for wood construction material compared with imported OSBs, but it is necessary to suggest reasonable design standards through additional performance verification as a structural panel material.