1. INTRODUCTION
Non wood fibers are usually classified as natural plants, industrial crops, and agricultural crops, which have various types, properties, and chemical compositions (Mohanty et al., 2005). Based on their characteristics, natural fibers are potential material for composite board. Many natural fibers have been investigated as raw materials for making composite board. Those materials include bamboo, elephant grass, sanseviera, kenaf, sisal, sorghum, sugarcane bagasse, ramie, etc (Grigoriu et al., 2000; Ndazi et al., 2006; Munawar et al., 2007; Kusumah et al., 2016; Rao et al., 2007; Widyorini et al., 2016). One of potential non-wood fiber that is still underutilized is elephant grass (Rao et al., 2007). Elephant grass has tensile strength of 185 MPa and modulus of 7.4 GPa and could be increased by 58 and 41%, respectively, by alkali treatment (Rao et al., 2007). Its low density and good thermal insulating properties made elephant grass a suitable composite material for light-weight structures (Rao et al., 2007; Ramanaiah et al., 2012).
Because of its high productivity, elephant grass is also utilized as the main food source for captive elephant. Digestibility of elephants was estimated to be 30~45% (Meissner et al., 1990) or around 55~70% of fibrous food consumed by an elephant is excreted undigested. According to Cavendish (2010) in Farah et al. (2014), an elephant can produce dung up to 110 kg per day. Farah et al. (2014) stated that elephant dung fibers contain high alpha cellulose which is to be a potential raw material for paper. Such properties also indicates that elephant dung fibers may also be a prospective composite material.
Since the recent reclassification of formaldehyde as carcinogenic to humans by International Agency for Research on Cancer (IARC, 2012), the acceptable levels of formaldehyde emission from wood panel products became stringent. Therefore, the developement of natural adhesives using biomaterial has been an attractive topic in recent years. Various biomaterials have been studied as natural adhesive, such as tannin (Pizzi, 2006), corn-tannin (Moubarik et al., 2013), lignin-tannin (Mansouri et al., 2011; Nasir et al., 2013), tannin and sucrose (Zhao and Umemura, 2014), glucose and sucrose (Tondi et al., 2012; Lamaming et al., 2013), as well as citric acid (Umemura et al., 2011; Widyorini et al., 2016).
Application of citric acid have been done in previous researches as a cross link agent for solid wood (Vukusic et al., 2006; Hasan et al., 2007), an absorber for heavy metal ions (Thanh and Nhung, 2009), and a cross link agent for starch film (Reddy and Yang, 2010). Citric acid has also been studied as a bonding agent for composite boards made from wood and bark (Umemura et al., 2011, Umemura et al., 2012), various bamboo species (Widyorini et al., 2016), oil palm frond (Widyorini et al., 2012), as well as sorghum bagasse (Kusumah et al., 2016). The results showed that citric acid-bonded particleboards provided high physical and mechanical properties. The ester linked between hydroxyl groups and carbonyl groups improve the performance of the boards (Umemura et al., 2012; Widyorini et al., 2016) and reduces the hygroscopicity of wood as well as the tendency to swell or shrink (Vukusic et al., 2006). The hydroxyl groups usually come from hemicellulose, but it supposed to come from cellulose or lignin as well. Elephant dung fibers contain relatively high lignin content (Farah et al., 2014), therefore it is interesting to analyze the properties of citric acid bonded board made from elephant dung. The chemical compositions of the raw materials may also affect the pressing temperature of the composite boards. This problem is one important point for application in wood industry. Therefore, this paper was designed to investigate the characteristic of board made from elephant dung fibers which bonded using citric acid with various contents and pressing temperature.
2. MATERIALS and METHODS
Elephant dung fibers were collected from Taman Safari Indonesia (TSI) II, a safari park in Pasuruan District, East Java, Indonesia. The fibers were then screened and those passed through on 10 mesh were used as board materials.
All of the fibers were air-dried to a moisture content of around 12%. The bulk density of fibers dried at 105°C for 24 h was determined by calculating the ratio of the mass to the volume occupied (Kusumah et al., 2016). First, a box with the dimension of 10 cm×10 cm×10 cm was weighed. Fibers were added to the box without any press until they reach the top of the box, and the box was then reweighed. The difference of the both weight was divided by the box volume, defined as the bulk density.
The distribution size of the materials was calculated as follows. A sample of dry fibers of known weight was separated through a series of sieves (10, 40, 60, and 100 mesh) with progressively smaller openings. Once separated, the weight of particles retained on each sieve was measured and compared to the total sample weight. The size distribution was then expressed as a percent retained by weight on each sieve size.
Citric acid (anhydrous), made from Weifang Ensign Industry Co. Ltd. China, was used without further purification. No other chemical compounds were added. Citric acid was dissolved in water under a certain ratio, and the solution concentration was adjusted to 59~60 wt%. The pH and viscosity of the solution at room temperature were 0.85 and 9.45 mPas, respectively.
The citric acid solution was sprayed onto fibers at various contents (10 wt%, 20 wt%, and 30 wt%) based on the weight of the dried fibers. The sprayed fibers were then oven-dried over night at 80°C to reduce moisture content to be around 3~5%. The fibers were hand-formed into a mat by using forming box (25 cm×25 cm), followed by hot pressing into compositeboard. The boards were pressed at 180°C and 200°C for 10 min under a pressure of 3.5 MPa. Binderlessboards (0 wt%) were also produced using the same condition. To obtain binderlessboards, dried fibers were directly hand-formed into a mat (Widyorini et al. 2005). The target thickness and the target board density were set at 1 cm and 0.8 g/cm3, respectively. Three replications were applied in this study. Prior to the evaluation of the mechanical and physical properties, all of the boards were conditioned at ambient conditions for about 7~10 days.
After being conditioned, the boards were then evaluated basically according to the Japanese Industrial Standard for Fiberboards (JIS A 5905, 2003). Tests were carried out for mechanical and physical properties, such as, thickness swelling (TS), water absorption (WA), modulus of rupture (MOR), modulus of elasticity (MOE), and internal bond (IB) strength. Surface roughness (Ra) was also evaluated in this research.
The static three-point bending tests in dry and wet conditions were conducted on a 20 cm×5 cm×1 cm specimen for each board. The effective span and loading speed were 15 cm and 1 cm/min, respectively. Before the bending strength test, the specimens were tested for their surface roughness using surface roughness SRG 4000. The average roughness (Ra) was then used to evaluate roughness characteritics of the fiberboards. Six measurements were randomly taken from both surfaces of each samples. The wet bending test was conducted according to wet bending strength test B. The specimens were immersed in boiling water for 2 h and immersed further in water at normal temperature for 1 h. The test was carried out as the specimen was still wet. The IB strength test was performed on a 5 cm×5 cm×1 cm specimen from each board. The same specimen dimension from each board was also prepared for TSWA tests after water immersion for 24 h at 20°C. The MOR, MOE, and IB strength of the boards values were then corrected for each target density based on specimen densities. Each experiment was performed in triplicate, and the average value and standard deviation were calculated.
The specimen of 5 cm×5 cm×1 cm from each treatment was used for image analysis of adhesives distribution on board surfaces. Images of wood fibers were recorded under a light microscope (Olympus BX 51; Olympus Coorporation; Japan) with a digital camera (Olympus DP 70; Olympus Coorporation; Japan). The dark coloration distributions on board surfaces that presented the ratio of dark area to total surface area, were measured with image-analysis software (Image pro Plus). The dark or black coloration is assumed as the presence of adhesives in unit area of board surfaces, as well as the degradation or modification of materials during treatment.
The wet bending strength test specimen was used as sample for FTIR anaysis. The materials were then dried at 40°C overnight and ground into a powder. All infrared spectras were obtained with FTIR spectrophotometer (Shimadzu IR Prestige-21) using KBr disk method and were recorded by means of an average of 10 scans at a resolution of 16 cm-1.
3. RESULTS and DISCUSSION
The bulk density of the elephant dung fibers was 0.110 ± 0.002 g/cm3. This value was relatively similar with other agricultural plants, such as kenaf core chips (0.118 g/cm3) (Grigoriu et al., 2000) sorghum bagasse (0.125 g/cm3) (Kusumah et al., 2016), and flax chips (0.09 g/cm3) (Papadopoulos and Hague, 2003). The bulk density of the elephant dung fibers was around to be about half that of the wood chip furnish (Papadopoulos and Hague, 2003). The distribution size of elephant dung fibers can be shown in Table 1. It showed that around 79.19 wt% of the fiber passed 10 mesh and is retained 60 mesh, while only 20.81 wt% of the fibers passed 60 mesh.
Size | wt% |
---|---|
Passed 10 mesh retained 40 mesh | 48.73 |
Passed 40 mesh retained 60 mesh | 30.46 |
Passed 60 mesh retained 100 mesh | 15.09 |
Passed 100 mesh | 5.72 |
It was interesting results that no delaminations were found in all the boards, even the color of the boards became darker with increasing the pressing temperature and citric acid contents. The same result was also found by Widyorini et al. (2016). It supposed due to a high degree hydrolysis or other modification of chemical components occured during treatments, resulting in more darker color. Table 2 shows thickness swelling and water absorption of the composite boards with various citric acid contents and pressing temperatures. It was clearly shown that all of binderlessboards had poor dimensional stability. After addition of 30 wt% citric acid and pressed at 180°C, it met the requirements of JIS A 5905 (TS max 12% for type 25). However, when the pressing temperature increased to 200°C, the minimum addition of citric acid was only 20 wt% to get good water resistance. It clearly showed that the pressing temperature and citric acid content affected simultaneously on producing high dimensional stability of the boards. Based on Umemura et al. (2012), it was clarified that the moulding developed water resistance at temperatures above 180°C and the water resistance improved with increasing moulding temperature. As mentioned by Vukusic et al. (2006), cross-linking chemicals reacting with hydroxyl groups reduced the hygroscopicity of wood and the tendency to swell or shrink.
The same trend was also found at the water absorption value of the boards. The binderless composite board has poor water resistance, which the WA was 271%. However, it clearly showed that increasing pressing temperature and citric acid content could decrease the water absorption or improve the dimensional stability of the boards, as also found by Umemura et al. (2012) and Widyorini et al. (2016). It indicated that increasing of ester linkages between carboxyl groups from citric acid and hydroxyl groups from lignocellulosic materials could decrease the free hydroxyl groups, therefore the composite boards became more hydrophobic.
Table 2 shows the surface roughness (Ra) value of elephant dung fibers at various citric acid contents and pressing temperatures. The average Ra values for binderlessboards range in 15.66~18.81 μm, while citric acid bonded composite boards range in 5.97~10.65 μm. Table 2 clearly shows that citric acid bonded composite boards have smoother surface compared to binderlessboards. The average Ra values ranged from 3.67 to 5.46 μm for commercially manufactured particleboard (Hiziroglu and Suzuki, 2007). Compared to that study, the composite boards made from elephant dung fibers with 30 wt% citric acid content was a little higher in Ra values. In addition to adhesive content, it mentioned by Nemli et al. (2005) that the surface quality of the particleboard is also a function of raw material type, pressure, board density, as well as shelling ratio.
Fig. 1 shows modulus of rupture of composite board at various citric acid contents and pressing temperatures. The modulus of rupture of binderlessboards was around 5.9 MPa, and increased significantly with addition of citric acid. However, increasing of citric acid content slightly increased the modulus of rupture. Interesting result was found, i.e. all of the citric acid bonded composite boards could meet the requirements of JIS A 5905 type 5 for fiberboards. In addition, for composite boards that pressed at 200°C and 30 wt% citric acid content can meet the requirement of type 15, i.e. more than 15 MPa.
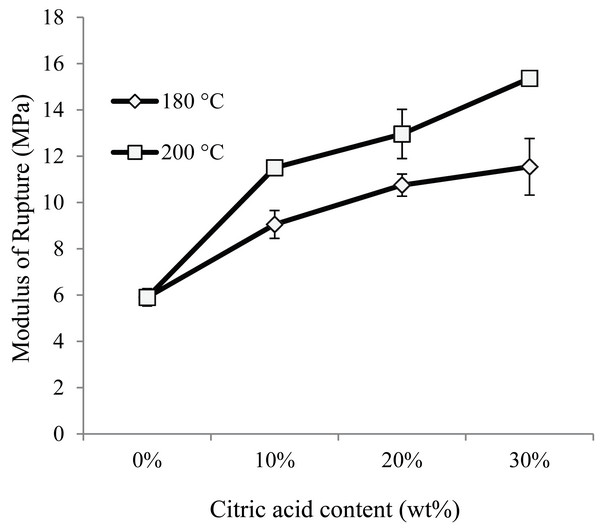
Increasing of pressing temperature caused significantly improved the modulus of rupture. This result consistent with the dimensional stability of the composite boards. It was clear that pressing temperature is also one important point for reaction between carboxyl groups and hydroxyl groups to make ester groups, as stated by McSweeny et al. (2006). However, Umemura et al. (2012) found that the pressing temperature above 180°C caused a decrease in bending properties of wood-based moulding bonded with citric acid. Based on those results, it was supposed that chemical composition of materials affected the optimal pressing temperature that required.
The same trend to modulus of rupture was also can be found on modulus of elasticity of the boards (Fig. 2). Addition of citric acid improved the modulus of elasticity around 2~3 times or more than 1.3 GPa, that is required for JIS A 5905 type 15. The highest modulus of elastictity in this research could be achieved at pressing temperature of 200°C and 30 wt% citric acid addition (3.4 GPa), which the value could meet the requirement of JIS A 5905 type 30, i.e. more than 2.5 GPa.
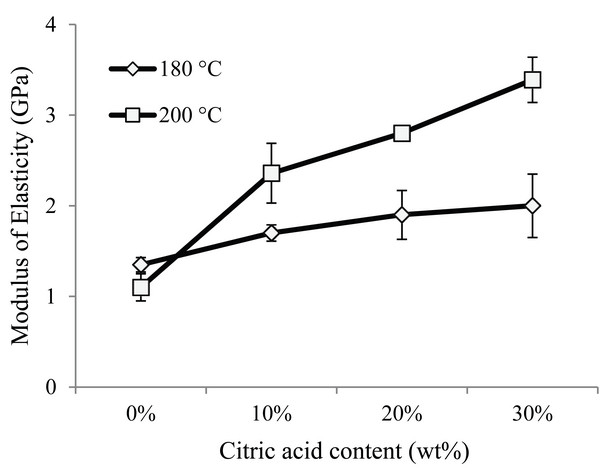
The wet bending tests of the composite boards are shown in Fig. 3. All of the binderlessboards were broken into pieces after immersion in boiling treatment for 2 h. It indicated that binderless boards had not any water resistance and low bending properties, as shown in Table 2 and Fig. 3, respectively. However, it showed that the citric acid bonded composite board had high water resistance and it was clearly affected by citric acid contents and pressing temperatures. According to JIS A 5905, bending strength under wet condition of 20 wt% and 30 wt% citric acid bonded composite board that pressed at 200°C met the standard type 15 (more than 7.5 MPa). This result showed that elephant dung fibers could be a prospective materials for making composite board.
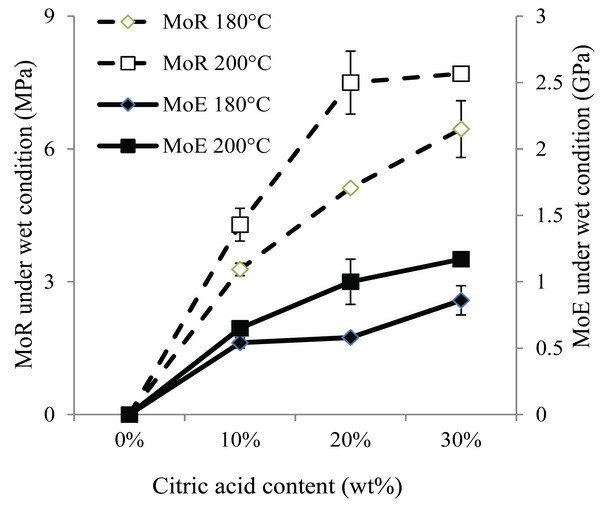
Internal bond strengths of the boards at various citric acid contents and pressing temperatures are shown at Fig. 4. Binderlessboards had almost no mechanical strength. Addition of citric acid 10 wt% improved internal bond strength almost 15 times compared than binderlessboards. All of citric acid bonded composite boards that pressed at temperature of 200°C, had internal bond strength more than 0.2 MPa, as required JIS A 5905 type 5. However, the boards that pressed at temperature of 180°C need 20 wt% of citric acid to achieve the internal bond strength that met the requirement of JIS A 5905 type 5. The highest internal bond strength was achieved after addition of 20 wt% citric acid and pressing temperature of 200°C, which the value of internal bond strength was 0.35 MPa and met the requirement of JIS A 5905 type 15. The boards had also good water resistance, indicating that the adhesive system had excellent bond performance, as shown in Table 2. The board with 30 wt% at 200°C had lower internal bond strength and higher modulus of rupture than that of the board with 20% at the same pressing temperature. However, at pressing temperature of 180°C, the bending and internal bond strengths of the boards increased with increasing of citric acid content, eventhough the values of the strengths were lower than that were pressed at 200°C. Widyorini et al. (2016) produced bamboo particleboards that had higher internal bond strength compared to elephant dung composite boards at the same condition of 180°C pressing temperature and 30 wt% citric acid. Compared to the bamboo particleboards, it was predicted that the chemical composition and materials types of the raw materials influenced the properties of the boards.
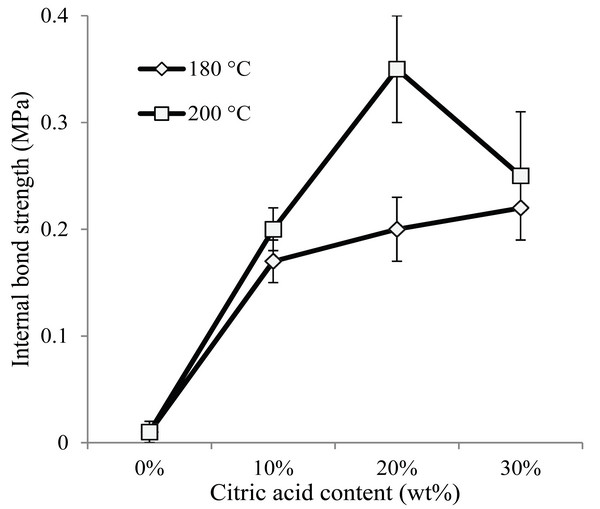
Fig. 5 shows binary images of light micrographs of board surface in various adhesive contents. Binary images were modified from light micrographs of board surface. In binary images, dark coloration is assumed as the presence of adhesives in a unit area of board surface, although it is also supported by the degradation or modification of its chemical components during pressing treatment. The dark coloration distribution that presented the ratio of dark area to total surface area, at various citric acid contents and pressing temperatures are shown at Table 3. The distribution of dark area in this study ranged from 2.06% to 43.02%. Fig. 5 showed that there are a few dark colorations in the surface of binderlessboards in both of 180 and 200°C. It mentioned in this paper, that no delaminations were found in all the boards, even in the binderlessboards. A few dark coloration of binderlessboard (0 wt%) was assumed due to the modification of chemical components occured during treatments or degradation of hemicellulose during pressing (Widyorini et al., 2005), therefore the binderlessboards could be produced even with low properties. The dark coloration distribution increased with increasing of citric acid contents and pressing temperatures. We found that the highest distribution of dark coloration was the samples with 30 wt% citric acid content and pressing temperature of 200°C, eventhough it was not remarkable different with the samples of 20 wt% at the same pressing temperature. These results were consistent with surface quality of the boards.
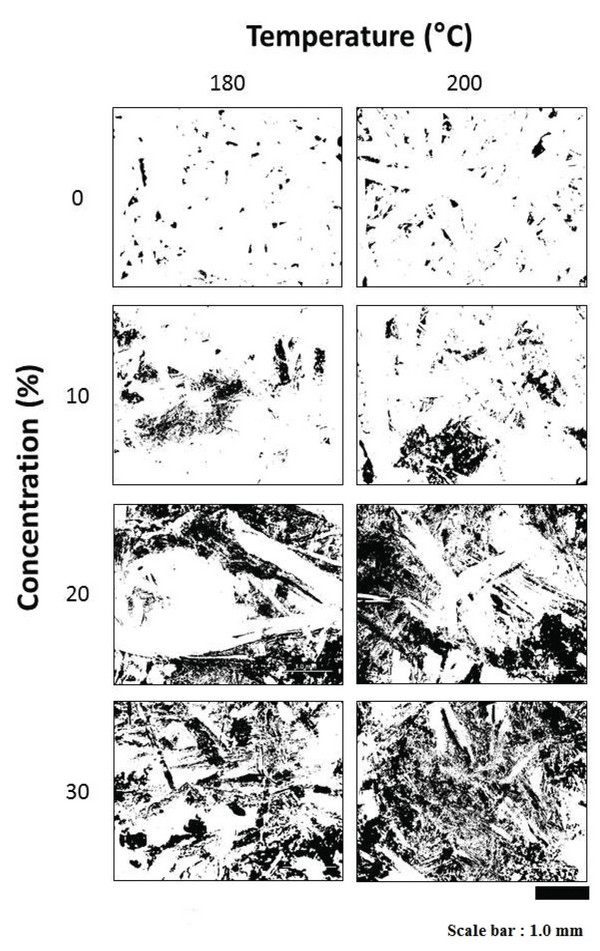
Citric content (wt%) | Temperature (°C) | |
---|---|---|
180 | 200 | |
0 | 2.06 ± 0.57% | 3.42 ± 0.92% |
10 | 9.82 ± 0.67% | 14.18 ± 2.29% |
20 | 28.08 ± 3.10% | 36.93 ± 1.07% |
30 | 28.78 ± 2.63% | 43.02 ± 3.45% |
The dark coloration of samples with pressing temperature 200°C showed higher distribution compared to the samples with pressing temperature 180°C, under the same adhesive content. It was supposed due to a high degree hydrolysis or other modification of chemical components occurred during treatments, as mentioned before. In addition, Umemura et al. (2012) mentioned that increasing pressing temperature caused increased of ester linked between carboxyl groups from citric acid and hydroxyl groups from lignocellulosic materials, resulting good bonding performance.
Fig. 6a shows an FTIR analysis of binderless board and citric acid bonded composite boards at various citric acid contents. The low intensity peak was indicated on the raw materials and binderlessboards (0 wt%), and it increased with increasing citric acid content, as shown in Fig. 6a. It was predicted that the low intensity peak at around 1,734 cm-1 on the raw materials was ascribed to C=O stretching derived from carbonyl groups (Umemura et al., 2012). In addition, C=O stretching in binderlessboard also was could resulted from the degradation of hemicellulose during pressing, as mentioned by Widyorini et al. (2005). As mentioned by Umemura et al. (2012), the peak at around 1,734 cm-1 on citric acid bonded composite board was attributed to C=O strecthing derived from C=O ester group, which resulting from the reaction between wood and citric acid. Fig. 6b shows that increasing of the pressing temperature remarkable affected the intensity of the carbonyl groups at the same level of citric acid content. It clearly showed that the formation of ester linkages as a result of the reaction between citric acid and hydroxyl groups would result in good mechanical and better dimensional stability of particleboards, as indicated in Figs. 1~4.
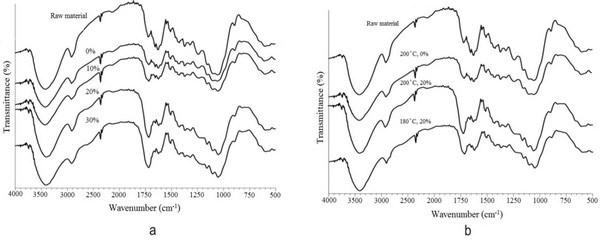
Based on Farah et al. (2014), fibers of elephant dung contain around 30 wt% of unsoluble lignin. It is predicted that lignin also contributed to the formation of the bonding mechanisms. There was not remarkable change in intensity of the peak at approximately 1,512 cm-1, which was recorded as C=C groups come from the aromatic unit of lignin (Okuda and Sato, 2004). However, further research on bonding mechanism of citric acid as an adhesive with lignin-rich materials will be studied.
4. CONCLUSION
Increasing pressing temperature and citric acid content improved significantly the dimensional stability of the board made from elephant dung fibers. Optimum condition in this research was achieved at pressing temperature of 200°C and 20 wt% of citric acid content. The properties of the composite board at the condition were as follows; the average thickness sweeling, water absorption, surface roughness, modulus of rupture, modulus of elasticity, modulus of rupture under wet condition, modulus of elasticity under wet condition, and internal bond strength were 10.45%, 52.6%, 7.8 μm, 12.96 MPa, 2.8 GPa, 7.5 MPa, 1 GPa, and 0.35 MPa, respectively. Based on these results, composite board made from elephant dung fibers and citric acid has great potential to be developed.