1. INTRODUCTION
Oil palm is an abundant source of biomass in Indonesia. In 2013, oil palm plantation has reached a total area of 6.2 million hectares or an increase of 16% from that of the 2010 (BPS 2014). Productivity of oil palm decrease at the age of 20 to 25 years (Kosugi et al., 2010; Prawitwong et al., 2012) and after felling the trunk is wasted or burnt at site (Yamada et al., 2010). Oil palm is generally planted with the planting density of 128 to 148 plants/ha (Lamaming et al., 2014) and with the average diameter of 40 cm and the stem length of 10 m, the amount of biomass produced will be approximately of 160-185 m3/ha. Therefore, an enormous biomass potential is available and possibly useful for the production of various valuable bio-products.
Oil palm stem retains low dimension stability and various types of defects such as raise grain, warping, and collapse after drying process that demands appropriate modification to improve its usefulness (Dungani et al., 2013). Production of biopellet is possibly another potential utilization of oil palm biomass. Successful conversion of the biomass into biopellet will contribute to the new renewable source of green energy.
Pellet utilization and technology has gained popularity in developed countries. The advantages of converting biomass into biopellet include the reduction of ash emission, storage convenience, and increasing biomass density (Carroll and Finnan, 2012).
Density (unit density or bulk density), moisture content, durability, and ash content are considered as important parameters for biopellet as the source of green energy (Theerarattananoon et al., 2011). Low density biopellet can increase transportation cost and storage capacity. Ash content will influence the formation of slag, bring about an inhomogeneous combustion, and be deposited after combustion process (Obernberger and Thek, 2004; Temmerman et al., 2006). An 11-50% decrease in durability is known to be occurred during storage when the moisture content of biopellet is over 10% (Tabil, 1996).
Durability is an important pellet parameter (Carroll and Finnan, 2012; Lee et al., 2013; Temmerman et al., 2006). Kaliyan and Morey (2009b) defined pellet durability as the capability of pellet to withstand the effect of shock, pressure, and friction during pellet handling and transportation. It is influenced by raw material factors (chemical component, moisture content, particle size, and raw material formulation), preconditioning factors (preheating and adhesives), pelletizer, and post pelleting condition. The contribution of raw material formulation, particle size, steam conditioning, die pellet mill, and cooling on pellet durability were 40, 20, 20, 15, and 5%, respectively (Thomas et al., 1997). Inter-particle bonding in pellet due to temperature and pressure (Filbakk et al., 2011; Lee et al., 2013), raw material crystallization, chemical reaction, and adhesive or lignin hardening after densification (Kaliyan and Morey, 2010) plays an important role in the durability of pellet.
Chemical components other than lignin, such as extractives, starches, and sugars also influence the characteristics of pellet. Extractives decrease the compressive strength (Stelte et al., 2011), but increase the calorific value of pellet (Telmo and Lousada, 2011). Starches (Lehmann et al., 2012) and sugars (Lamaming et al., 2014) can function as adhesive that improves the inter-particle adhering of pellet.
The present work was intended to investigate the effect of chemical components and bark content on OPT-based pellet prepared at various pelleting temperature and pressure. The durability, moisture content, density, ash content, and calorific value of the resulted OPT-based pellet were measured.
2. MATERIALS AND METHODS
A 25 years old oil palm stem was divided into its bottom, middle and upper divisions. All divisions were debarked and chipped. The chips were then refined with Wiley mill and sieved to result in powder of 20-40 mesh and 40-60 mesh. The powder of 40-60 mesh was used for chemical analysis following the standard procedures of TAPPI T 257 om-85, and the powder of 20-40 mesh with adjusted moisture content to 8-10% was used for pellet preparation following the work of Kaliyan and Morey (2009a).
The content of extractives, holocellulose, Klason lignin, α-cellulose, and ash of the oil palm trunk was analyzed in accordance with the standard procedures explained in TAPPI T 204 om-88, Browning (1967), Dence (1992), TAPPI T 203 os-94, and TAPPI T 211 om-93, respectively. Hemicellulose content was calculated by subtracting α-cellulose content from holocellulose.
Densification of oil palm biomass was carried out using a pellet mill (plane diameter of 1.6 cm) with densification pressure of 10.3 MPa. Bark content and densification temperature of the prepared pellet were varied. Bark content was at 0, 10, and 30% of the total weight of pellet and densification was carried out at 130, 160, and 190°C. Total densification time was 6 min consisting of 3 min preheating and 3 min densification in accordance with that carried out by Kaliyan and Morey (2009a) and Lee et al. (2013).
The moisture content of pellet was determined by oven drying method at 103 + 2°C, and pellet density was determined in the basis of displacement method previously applied by Rabier et al. (2006). The ash content of pellet was determined in accordance with the standard procedures of TAPPI T 211 om-93 and its durability was measured in accordance with ASABE standard (2003) (Fasina, 2008). The calorific value of pellet was measured with Bomb Calorimeter LECO UK AC-500.
Visual information of interparticle bonding was procured by scanning electron microscopy (SEM, JSM-6510LV, JEOL USA) with 50x and 500x magnification. Thermal properties of pellet with 0% and 30% bark content were determined by TG-50 (ZG-127, Shimadzu). In the thermal analysis, 3-6 g of samples were analyzed in the range of 30-600°C at heating rate of 10°C/min. Alumina (α-Al2O3) powder was used as control.
The resulted data of the present research were analyzed with factorial complete random design with two factors, i.e. bark content and densification temperature. The data were procured in triplicate. Further Duncan’s multiple range test was also carried out for the data.
3. RESULTS AND DISCUSSION
Table 1 indicates the chemical composition of oil palm stem. Holocellulose, lignin, and ash content were not significantly different in bottom, middle, and upper divisions of oil palm meristem. However, they were different from those of its bark. The content of holocellulose of the oil palm meristem was higher than that of its bark. Lignin content of oil palm stem was lower than that of its bark, similar to the finding of Chow et al. (2008) for the guayule wood. Oil palm meristem and bark contained similar amount of extractives, showing 7.63-9.25%. Extractives generally have an opposing effect on biopellet quality. Its element tends to bring about increasing calorific value of pellet (Filbakk et al., 2011) but hinders the satisfying formation of inter-particle bonding (Stelte et al., 2011), resulting in a commonly less durable pellet. The ash content of meristem was significantly lower than that in its bark. The main minerals are considered to be Cl, Ca, Mg, and Na (Kosugi et al., 2010).
Fig. 1 shows the effect of bark content and densification temperature on the durability of OPT-based pellet. Compared to the requirement of DIN EN 14961-2 A2 standard, the durability was very lower, showing less than 50%. This value is significantly lower than a minimum value (97.5%) required by the standard. Bark content increased the durability, but the durability was increased with increasing densification temperature. Factors such as particle size, raw material compositions, densification temperature and pressure are known to influence the durability of pellet. Lee et al. (2013) produced Larix kaempferi wood-based pellets with high durability (> 97.80%) using only densification pressure of 1.5 MPa.
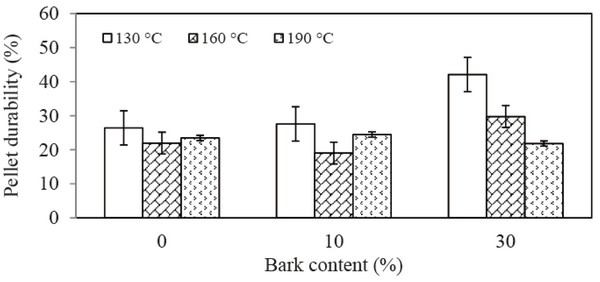
Table 2 Duncan’s multiple range tests for the effect of bark content on the durability, moisture content, density and densification temperature of OPT-based pellet. Bark content influenced pellet durability (p < 0.05). Duncan’s multiple range tests indicates that bark content resulted in different pellet durability. Pellet with 30% bark content had the highest durability. The increasing amount of lignin due to bark addition was possibly the cause of increasing pellet durability. The influence of lignin on pellet durability has been reported by Lee et al. (2013). They found that the durability of Larix kaempferi wood pellet with 32% lignin content was higher than that of Liriodendron tulipifera wood pellet with lignin content of 22%. Pellet prepared at 130°C resulted in the highest durability. The durability of pellet decreased with further increasing of densification temperature. Similar influence of densification temperature on durability of the pellet from corn stover and switch grass was previously reported by Kaliyan and More (2009c). Glass transition temperature (Tg) of lignin is considered critical for an appropriate densification temperature. Several different Tg of lignin has been reported, i.e. in the range of 52-117°C (Kaliyan and More, 2009c), ~130°C (Basu, 2010), and 100- 144°C (Tejado et al., 2007). Densification at temperature close to Tg of lignin will increase the distribution of natural adhesives such as lignin, starch, protein, and fat in pellet (Kaliyan and More, 2009c). However, lignin starts to decompose at temperature of above 140°C (Stefanidis et al., 2014, Kim et al., 2014). Therefore, binding capability of lignin will be possibly decreased when densification of pellet is carried out at more than 140°C.
Extractives are known to impede the formation of interparticle hydrogen bond in pellet (Stelte et al., 2011). According to Samuelsson et al. (2012), at more than 2.5% concentration of extractives, pellet durability decrease to lower than 95%. Therefore, high extractives concentration of 7.63-9.25% was thought to impair the durability of the resulted pellet.
Fig. 2 indicates the SEM micrograph of the surface of OPT-based pellet. The interparticle interlocking was shown even in pellet with higher durability (0% and 30% bark content at densification temperature of 130°C), indicating many gaps between particles. Low interparticle bonding was assumed to bring about low pellet durability. As reported by Kaliyan and Morey (2009a), the increase of pressing load could increase pellet durability, showing that densification pressure of 100-150 MPa is for a good pellet durability.
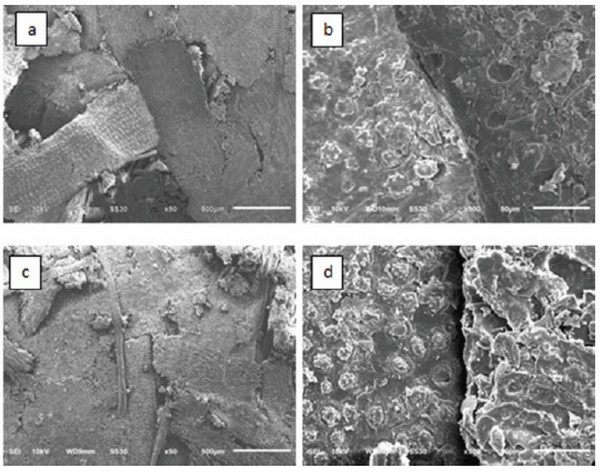
Fig. 3 shows the effect of bark content and densification temperature on moisture content of OPT-based pellet. The average moisture content of OPT-based pellet was of 3.55-5.35%. Table 2 indicates that the influence of bark content on moisture content is significant after the addition of 30% bark in pellet. The moisture content of the resulted pellet was in accordance with the requirement of DIN EN 14961-2 A2 standard, i.e. < 10%. Moisture content of pellet will influence its durability. According to Tabil (1996), the increase of moisture content above 10% during storage decreased pellet durability of 11-50%. In Table 2, pellet with higher bark content retained higher moisture content and the increase of densification temperature decreased the moisture content of the pellet (Fig. 3). Moisture content of pellet is known to be influenced by densification temperature and the moisture content of its raw material (Kaliyan and Morey, 2009c). The present finding also indicates that increase of moisture content in the raw materials increased the moisture content of pellet. The average moisture content of the raw material for the presently produced pellet was of 8.45%, 8.54%, and 9.24% for pellet with bark content of 0, 10, and 30%, respectively.
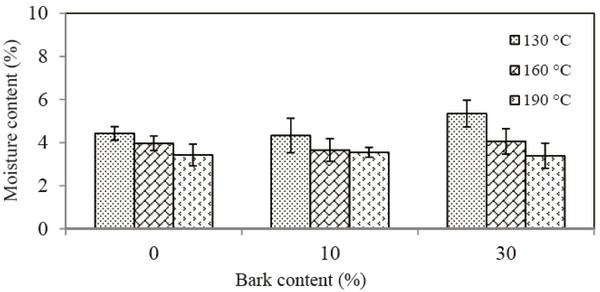
Fig. 4 shows the effect of bark content and densification temperature on density of OPT-based pellet. The obtained density was relatively low. Pellet density was influenced by bark content and densification temperature. A significant increase of density was resulted with increasing densification temperature. The average density of pellet produced in the present works was in the range of 525.56-855.23 kg/m3. A good pellet should has a density of more than 1000 kg/m3 (Obernberger and Thek, 2004). Duncan multiple range test of pellet density (Table 2) indicates that the presence of bark in pellet reduced its density. Extractives will increase the calorific value of pellet. However, they hinder interparticle bonding in pellet (Stelte et al., 2011). This might be the reason of reducing pellet density with the addition of bark in pellet preparation. Interparticle bonding can be also promoted by lignin flowing occurred at elevated densification temperature. As shown in Table 2 and Fig. 4, pellet density increased with increasing densification temperature, which is similar to the finding of Kaliyan and Morey (2010).
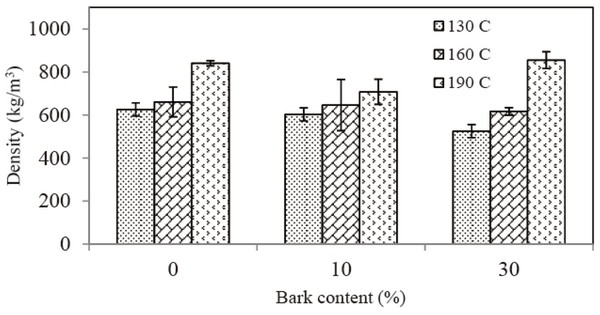
Pellet with high ash content is not acceptable for industrial use. Ash in pellet disturbs combustion system, bringing about slag formation and deposit, which needs to be frequently cleaned from combustion furnace (Obernberger and Thek, 2004). Fig. 5 shows the effect of bark content and densification temperature on ash content of OPT-based pellet. The average of ash content of the resulted pellet was very high compared, for example, with the requirement of DIN EN 14961-2 A2 standard. This standard requires ash content of 1.5% or below. A significantly higher ash content of pellet was found with the addition of 30% bark content (Table 2). The increase of ash content with increasing bark content certainly was brought about by the higher ash content of the bark than that of the oil palm trunk meristem. A similar effect on increasing bark content in pine wood pellet has been reported by Filbakk et al. (2011). Densification temperature did not change the ash content of pellet. This might be due to the inorganic component of biomass is more resistant to heat than that of its organic components.
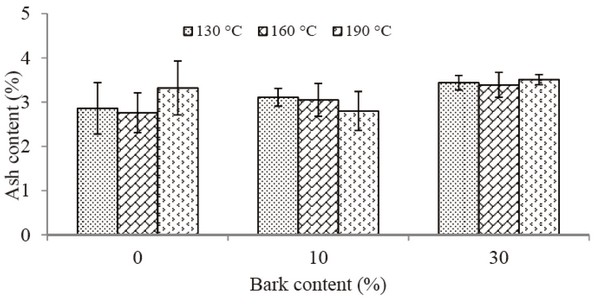
Fig. 6 show the effect of bark content and densification temperature on calorific value of OPT-based pellet. Calorific values of the resulted pellet were in the range of 17.89 - 19.14 MJ/kg. Therefore, the calorific value can be considered high as compared for example with the calorific value required by DIN 14961-2 A2 standard (16.3-19 MJ/kg). In average, increasing densification temperature tended to increase the calorific value. However, increasing bark content did not seem to increase the calorific value. Even though bark contains higher amount of lignin and extractives that are beneficial for the calorific value of pellet (Fillbakk et al., 2011, Ferre et al., 2014), its high ash content could impede the beneficial effect of lignin and extractive on the calorific value.
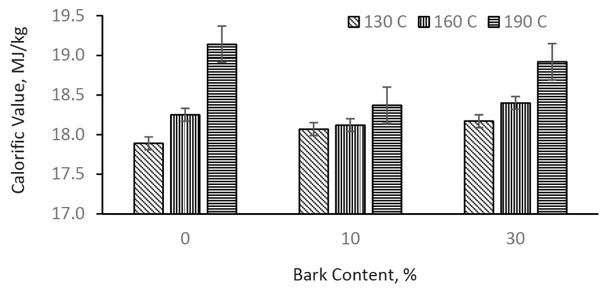
TG-DTA analysis was carried out for OPT-based pellet with 0% and 30% bark content (Fig. 7), indicating three stages of thermal degradation. Weight loss of oil palm trunk in each decomposition phase is summarized in Table 3. In the first phase, weight loss of about 5% occurred at 105°C, which is due to the loss of water (Yang et al., 2007, Pasangulapati et al., 2012). Weight loss (86-91%) was occurred in second phase, which may be due to the degradation of cellulose, hemicelluloses and lignin.
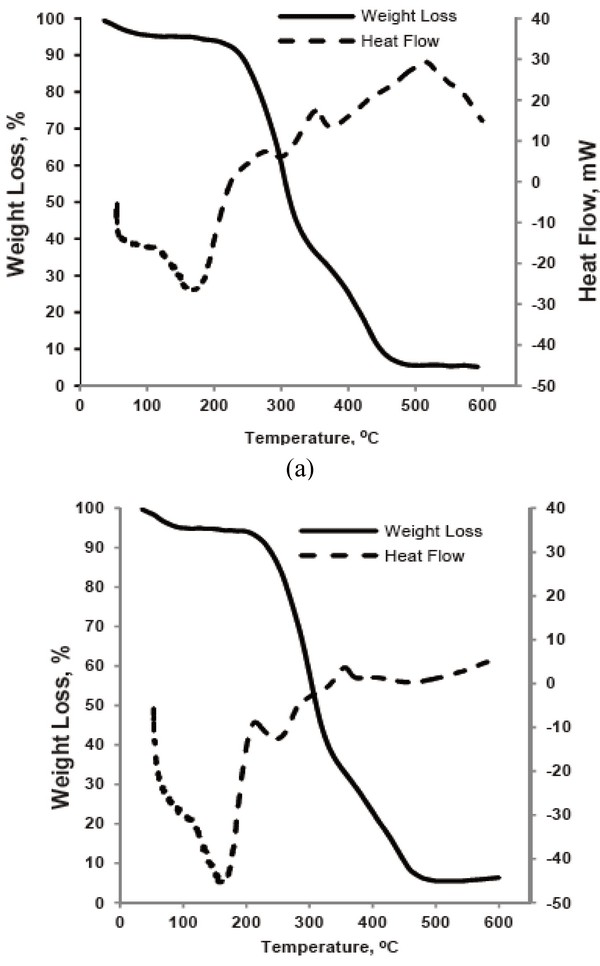
The DTA curve of pellet with 0% bark content indicates 3 exothermic reactions, i.e. at 243-272°C, 317-349°C, and 453-512°C. These exothermic reactions indicate the dominant decomposition of hemicellulose, cellulose, and lignin, respectively (Basu, 2010, Parthasarathy et al., 2013). For pellet with 30% bark content, endothermic and exothermic reaction occurred at 217-251°C and 333-354°C, respectively. Different endothermic and exothermic reaction temperature between pellet with 0% and 30% bark content possibly would be due to differences in the composition of their chemical components. Residual combustion proceeded at temperature over 470°C. A slightly higher residual combustion for the pellet with 30% bark content may be due to higher amount of ash in bark. Residual combustion is known to be influenced by the inorganic content of raw materials (Parthasarathy et al., 2013). The results of Fig. 7 also indicate that densification should be done at below 200°C to avoid mass loss during pellet preparation. Degradation of hemicellulose, cellulose and lignin could change many pellet properties. Pellet durability can be affected by hemicellulose, starch and lignin (Kaliyan and More, 2009c).
4. CONCLUSIONS
The durability of pellet was increased with increasing bark content and at densification temperature near Tg of lignin. Densification pressure of 10 MPa was not enough to develop a good interparticle bonding, resulting in poor durability. Addition of 30% bark increased the calorific value of pellet. It was found that densification should be done at below 200°C to avoid significant mass loss during pellet preparation.